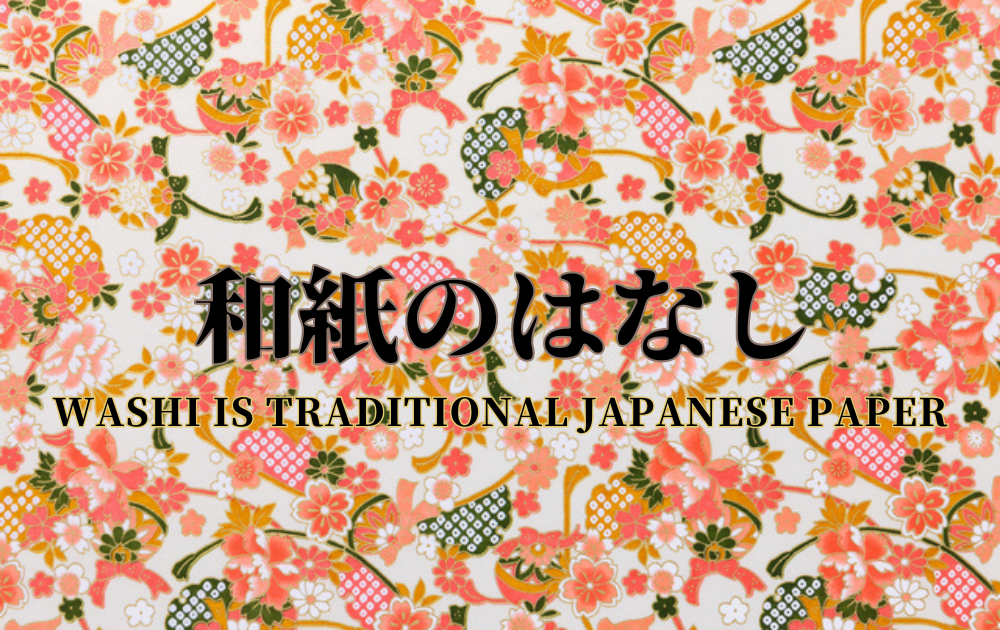
Washi is paper made using traditional Japanese techniques that date back centuries, utilizing materials such as kozo (mulberry), gampi, and mitsumata. During the Edo period, it was used not only for books but also for umbrellas, lanterns, and shoji (paper doors), becoming an indispensable part of people’s lives.
I am not aware of any other country where paper was so widespread before the industrialization of the paper-making industry. This time, we’re talking about washi, which you may know about but probably haven’t had much hands-on experience with.
What Exactly is Washi?
Washi is made from the fibers of plants such as kozo (mulberry), gampi, and mitsumata. The bark of these plants is boiled, beaten into a pulp to break it down into fibers, and then mixed with water and a sticky substance like neri from the tororo-aoi plant. It is then formed by spreading this mixture over a screen and shaking it to evenly distribute the fibers while the water drains through, intertwining the fibers to create the paper.
I’ve simplified the process, but in reality, there are many steps involved, and creating good paper requires precise skills and extensive experience.
The fibers of washi are longer and much more durable than those of Western paper, offering superior preservability. There is also a great deal of flexibility in thickness, allowing for the creation of paper that is thin enough to be translucent, as well as thicker varieties suitable for uses such as business cards.
Interestingly, in Europe, paper was also made by hand, but the materials used were primarily fibers from rags and similar sources. Perhaps due to early industrialization, it seems that now there are hardly any paper craftsmen left who use these ancient European methods.
However, upon research, I found someone in Germany who makes handcrafted paper using a unique method that combines European and Japanese techniques. I’ll provide a link for more information.
What kind of printing and processing can be done?
Although it’s difficult to generalize due to the variety of washi types, for example, machine-made washi that is suitable for printing can be used for offset printing. For handmade washi that may not have precise dimensions or has a less smooth surface, letterpress printing or silk screen printing can be done. If the washi is thick, it is also well-suited for foil stamping in addition to letterpress printing.
Die-cutting is also possible, but the method varies depending on the thickness of the paper. Extremely thin washi may not be suitable for automated machines, so it is better suited for die-cutting with a Vic or lay-down press.
When processing with a laser, depending on the type, there may be noticeable scorching or residue due to thickness irregularities. Testing is necessary beforehand for paper being processed for the first time.
As a point of caution, please be aware that with handmade washi, regardless of the type of printing or processing used, precise registration (alignment) cannot be guaranteed. Therefore, printing or processing requiring high precision may not be suitable.
Handmade Japanese paper from various regions of Japan
Despite being a very small portion of the overall paper production, including Western paper, washi still maintains a presence across various regions of Japan. I have picked out a few that are registered as cultural heritage. (The link will take you to the website of the Agency for Cultural Affairs).
[Echizen Torinoko Paper (Fukui Prefecture)] https://kunishitei.bunka.go.jp/bsys/maindetails/303/00000332
[Moto Minogami Paper (Gifu Prefecture)] https://kunishitei.bunka.go.jp/heritage/detail/303/122
[Ishizushi Hanshi Paper (Shimane Prefecture)] https://kunishitei.bunka.go.jp/heritage/detail/303/123
[Oguni Paper (Niigata Prefecture)] https://kunishitei.bunka.go.jp/heritage/detail/313/242
The Oguni Washi Production Cooperative provides an easy-to-understand introduction to the paper-making process. Please visit the following website! https://www.oguniwashi.com/blank-8
[Hosokawa Paper (Saitama Prefecture)] https://kunishitei.bunka.go.jp/heritage/detail/303/121
Surprisingly, the traditional art of Japanese paper-making also persists in Saitama Prefecture, where our company is located!
In fact, records indicate that paper-making has been practiced in Saitama Prefecture (formerly part of Musashi Province) since the Nara period. As described in the above text about Hosokawa Paper, areas such as Ogawa-cho in Saitama Prefecture, along with Hiki, Chichibu, and Otonami, flourished as major producers of washi during the Edo period. Even today, Ogawa-cho continues the tradition of paper-making under the name Ogawa Washi, honoring its long history.
In addition to Saitama, various types of washi continue to be produced across the country, with many preserving traditional manufacturing methods.
The Future of Washi
Kozo and mitsumata, which are the raw materials for washi, grow quickly and can be harvested without uprooting the plant. There is an image that making paper requires cutting down a large number of trees, but being able to harvest every year without killing the trees gives a very sustainable and SDGs-like feeling.
Despite its significance, the traditional Japanese paper industry is facing challenges such as stagnant production and an aging workforce. It is crucial for the culture of washi to thrive that it reaches as many people as possible.
This fiscal year, we have received an increasing number of requests for ‘kirie goshuin,’ traditional Japanese cut-paper stamps, and along with that, we have also received many requests to use washi or washi-style Western paper. As a specialist in paper processing, we aim to provide introductions to washi and washi-style Western paper, as well as propose various printing and processing methods suitable for these papers.
Why not create paper products using traditional yet innovative washi?