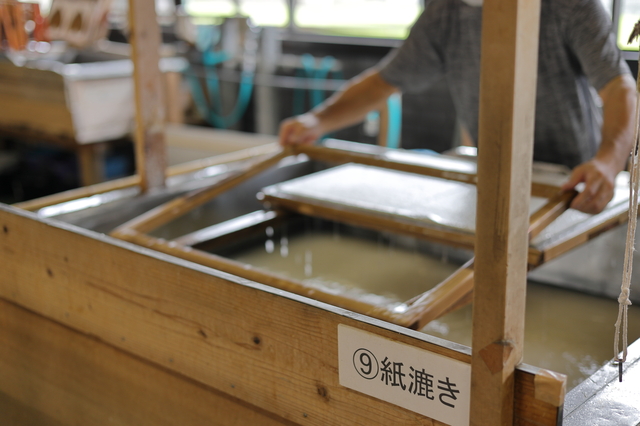
Washi is a traditional Japanese paper made using age-old techniques and materials such as kozo, ganpi, and mitsumata. In the Edo period, it was used not only for books but also for everyday items such as umbrellas, lanterns, and shoji screens, becoming an essential part of people’s lives. I don’t know of any other country where paper was so widely used before the industrialization of the paper industry. Today, let’s discuss washi, a type of paper that we might know but have never really handled before.
Table of Contents
What is Washi?
Washi is made from plant fibers such as kozo, ganpi, and mitsumata. The bark of these plants is boiled, broken down into fine fibers, and mixed with water and a paste made from plants like tororoaoi. The mixture is then screened, which involves evenly spreading the fibers in water and allowing them to interlock while the water is drained away. Although this process may sound simple, it involves many steps, and only skilled and experienced craftsman can make good-quality paper. Washi fibers are longer and more durable than those of Western paper, and they have excellent preservation properties. The thickness of washi can also be varied, ranging from thin, translucent sheets to sturdy, thick sheets suitable for business cards.
Handmade paper was also produced in Europe, but the primary materials were worn-out cloth and other fibers. As a result of the rapid industrialization of the European paper industry, there are currently very few papermakers who still use traditional European techniques. However, I found a papermaker in Germany who produces handmade paper using a unique technique that combines European and Japanese methods. Here is the link to their website.
https://papiergangolfulbricht.com/en/philosophy/
What Kind of Printing and Processing Can Be Done on Washi?
There are many types of washi, but for example, machine-made washi with good printability can be used for offset printing, while handmade washi with less precise dimensions and a less smooth surface can be used for letterpress or silk-screen printing.
Thick washi is also suitable for foil stamping in addition to letterpress printing. Die-cutting can be done on washi, but the method varies depending on the thickness of the paper. Thin washi may not be suitable for automatic machines, so semi-automatic machines or other press machines are recommended.
When processing washi with a laser, certain types may exhibit noticeable burn marks or have uneven thickness, which can result in incomplete cuts that occur randomly. Therefore, testing the paper beforehand is essential. As a note, when using handmade washi, don’t expect precise alignment for any printing or processing method; therefore, it’s not suitable for applications that require high accuracy.
Handmade Washi from Various Regions in Japan
Although washi makes up a small proportion of the total paper production, including Western paper, there are still many types of handmade washi made throughout Japan. I have picked up some examples registered as cultural heritage (links lead to the Cultural Affairs Agency’s website):
[Echizen Tori-no-ko Paper (Fukui Prefecture)]
https://kunishitei.bunka.go.jp/bsys/maindetails/303/00000332
[Hon-Mino Paper (Gifu Prefecture)]
https://kunishitei.bunka.go.jp/heritage/detail/303/122
[Sekishu Banshi Paper (Shimane Prefecture)]
https://kunishitei.bunka.go.jp/heritage/detail/303/123
[Oguni Paper (Niigata Prefecture)]
https://kunishitei.bunka.go.jp/heritage/detail/313/242
Oguni Washi Production Cooperative provides an easy-to-understand introduction to the paper-making process. Be sure to check out their website as well:
https://www.oguniwashi.com/blank-8
[Hosokawa Paper (Saitama Prefecture)]
https://kunishitei.bunka.go.jp/heritage/detail/303/121
Surprisingly, our company is located in Saitama Prefecture, where the tradition of washi-making still exists! In fact, records show that papermaking has been carried out in Saitama Prefecture (formerly known as Musashi Province) since the Nara period (AC710-794). As mentioned in the description of Hosokawa Paper above, the areas of Hiki, Chichibu, and Ogawa, with Ogawa Town as the center, thrived as a major washi production region during the Edo period. Even today, Ogawa Town continues to produce Ogawa Washi, inheriting its long history.
Various types of washi are still produced in many other regions across Japan, with numerous places committed to preserving traditional manufacturing methods.
The Future of Washi
The plants used to make washi, such as kozo and mitsumata, grow quickly and do not need to be uprooted during harvest. Although papermaking is often associated with large-scale deforestation, these plants can be harvested annually without killing the trees, which is very much in line with the SDGs. However, washi faces challenges such as stagnant production and an aging workforce. It is essential for more people to use washi in order to preserve this cultural heritage.
This year, we have received more requests for traditional paper-cutting designs, along with an increasing demand for washi or washi-style Western paper. As a specialist in paper processing, our company aims to introduce various types of washi and washi-style Western paper and propose suitable printing and processing methods for them.
Why not create unique paper products using washi, which may seem old but is actually quite new? For any inquiries about paper processing, please don’t hesitate to contact us through the inquiry form on our website!
“Turning ideas into reality.”