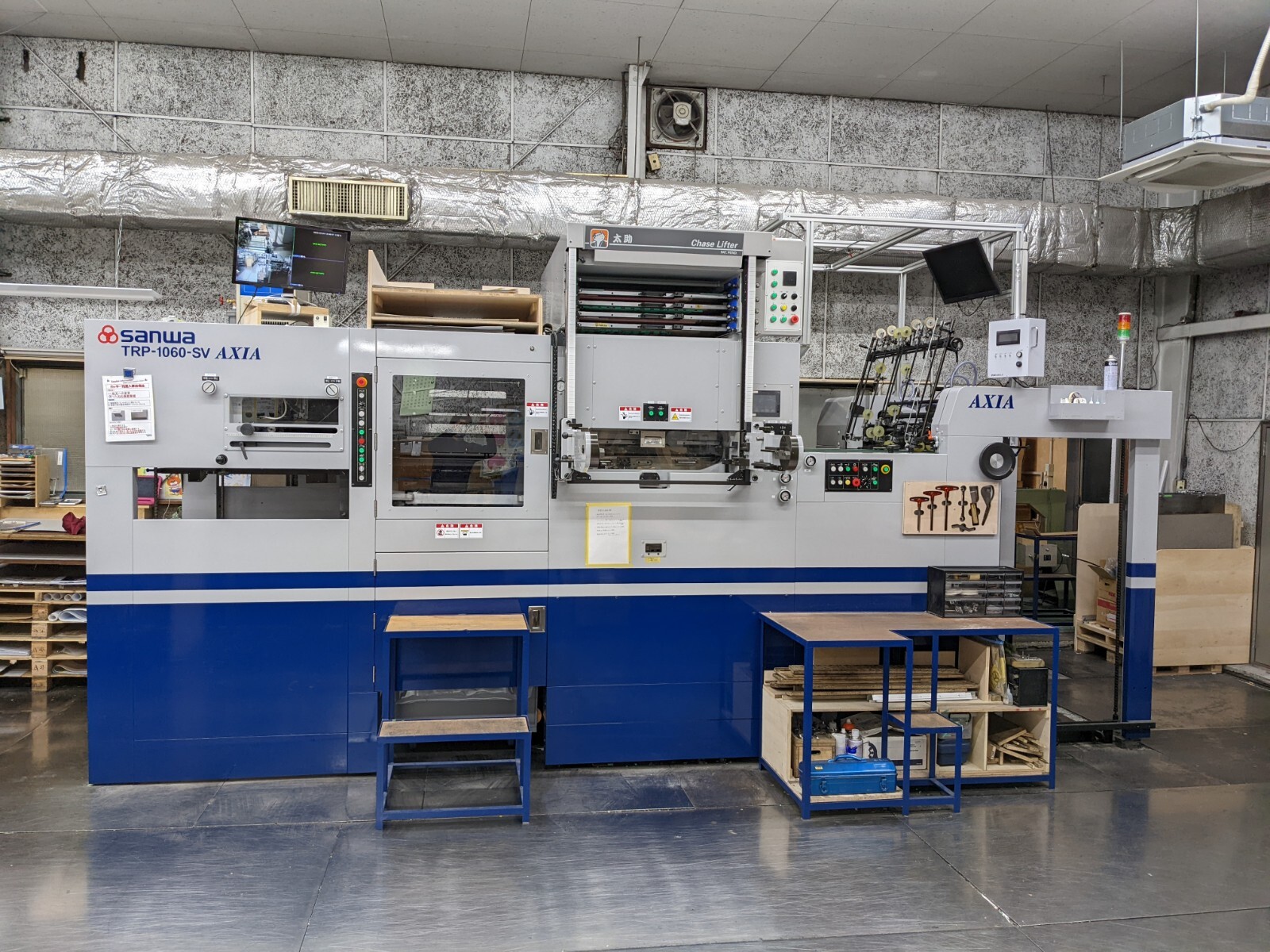
In printed materials processing, the choice of processing method is a crucial factor, as it significantly impacts the quality, cost, and efficiency of the final product.
At our company, we primarily use two paper processing methods: “punching” and “laser cutting.” This time, we will introduce the features, advantages, and suitable applications of each method.
Features of Punching
Punching (die-cutting) is a processing method that uses a die to cut paper. It allows large quantities of paper to be processed into the same shape according to the design of the die.
Processing is primarily done using wooden dies (also known as Thomson dies or Vic dies), but metal dies such as engraved or etched dies may also be used. This time, we will introduce the process using wooden dies with an automatic punching machine.
Merit
High productivity
It can process large sheets of paper printed with multiple layouts at once. With the ability to process 2,000 to 3,000 sheets or more per hour, it offers extremely high productivity.
Cost Efficiency
Although there is a cost involved in creating the die, the cost per sheet becomes lower in the case of mass production.
High-precision finish
Since a die is used, the same shape can be repeatedly processed with high precision. Additionally, the equipment includes a device that detects printing position accuracy, allowing processing to maintain high registration precision.
Disadvantages
High initial investment
Creating a die costs tens of thousands of yen or more, making the cost relatively high for small production runs.
Difficult to modify designs
To change the design, a new die must be created, making it difficult to accommodate sudden design or specification changes.
Features of Laser Processing
Laser processing is a method that uses a laser beam to cut paper by burning it. Using data created with design software such as Illustrator, it allows for precise and intricate processing. Additionally, it can be used not only for paper but also for materials such as wood, acrylic, and PET.
Merit
Flexible design adaptability
Since it does not require plates or dies, processing can be done directly based on the created data. This makes it easy to modify designs, and laser processing can reproduce complex and intricate shapes that are difficult to achieve with dies.
Low initial investment
Since no die is required, initial costs are reduced, making it highly cost-efficient for small production runs.
High-precision processing
It can accurately process fine details with a minimum line spacing of approximately 0.6mm. Additionally, even intricate shapes can be processed exactly as per the data, making it suitable for detailed designs.
Disadvantages
It takes time for mass production
Since the laser moves in a manner similar to a single-stroke drawing, the processing time per sheet tends to be longer compared to die-cutting, which can perform multi-surface processing in a single press. As a result, mass production may take more time.
Select the material
Laser processing involves burning through the material, which can cause charring or soot depending on the type of paper, potentially resulting in an unfavorable appearance.
Papers with coated surfaces, such as coated paper, or papers containing carbon or similar substances in their dye, such as black paper, are more prone to charring, discoloration, and soot formation.
Which one should I choose?
The choice between die-cutting and laser processing depends on the product’s characteristics, production volume, and design complexity.
In the case of mass production with simple shapes
Die-cutting is the best option
With our equipment, it is possible to process full-size sheets (800 x 1100 mm) directly, making it easy to handle multi-up layouts. This results in high productivity and lower cost per unit.
When fold lines are required
Die-cutting is more suitable
Unfortunately, laser processing cannot create fold lines. However, by replacing fold lines with perforated processing, laser processing can still be used.
In the case of small production runs or complex designs
Laser processing is the best option
Since no mold production is required, the cost can be reduced for small production runs.
For small production runs of paper crafts or more complex shapes, laser processing is recommended because it does not require initial mold costs and imposes fewer limitations on the shapes that can be created.
The balance between cost and quality
Ultimately, choosing the processing method should depend on carefully considering the balance between cost and quality.
Although die-cutting involves a high initial investment, it becomes cost-efficient for mass production, typically exceeding several thousand units, depending on the size and specifications.
In addition, a wide range of paper types can be processed, from thin paper (equivalent to 46/70kg for high-quality paper in our standards) to thick paper.
On the other hand, laser processing offers high flexibility in design and excels in reproducing complex shapes and small production runs.
However, it can take longer for mass production and may require extended lead times.
Additionally, depending on the type of paper being processed, quality issues such as discoloration or soot caused by charring and smoke residue may arise.
Summary
The choice between die-cutting and laser processing depends on factors such as the intended use, design, and production quantity. Therefore, it is essential to first identify the specific requirements of the project.
Both methods can be used to efficiently produce high-quality products by maximizing their respective advantages.