Everything About Paper Die Cutting Explained by a Paper Processing Company with 64 Years of Establishment [Part 3: The Die Edition]
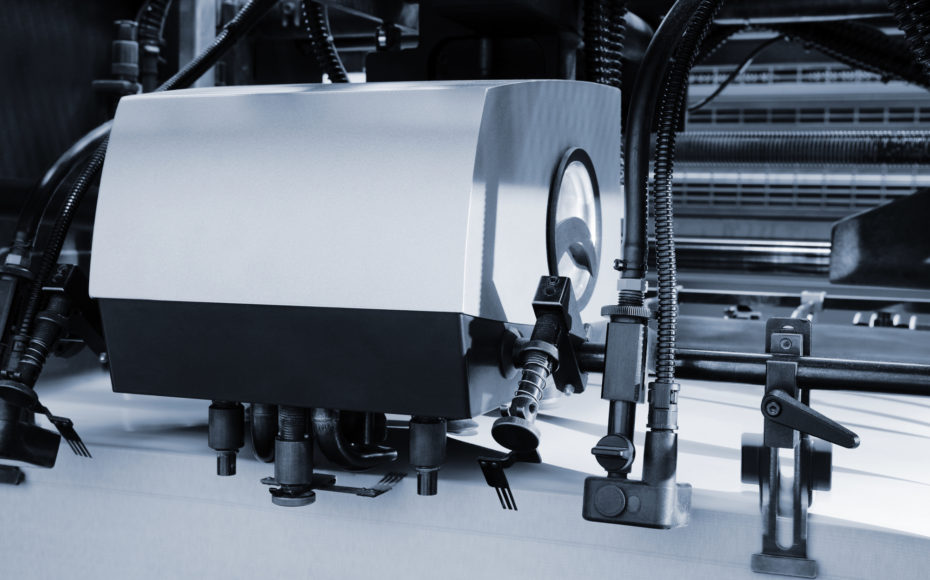
Table of Contents
It has been a quick two months since the last article… I was wondering why it had gotten so cold, and before I knew it, winter had arrived. We have kept you waiting for a long time, and here is the third installment of the die-cutting series. Thanks to your support, autumn was a busy time, and I hardly had the chance to pick up a pen (my excuse).
Types of Dies
Now, the paper die-cutting process that our company operates requires dies. These are essential for the flatbed automatic die-cutting machines we introduced last time, but what exactly are they?
There are various types of dies, including wooden dies, metal dies, etched dies, and engraved dies. Each type is used depending on the material and shape of the item being processed, as well as the method of processing. Additionally, each type of die is manufactured differently. Wooden dies are made by cutting slits into plywood using laser cutting or a jigsaw, and then inserting various types of blades such as creasing blades, cutting blades, and perforating blades.
Metal dies are commonly made by forging, where steel is heated and shaped, followed by sharpening and polishing, and finally, by hardening. In the case of Swedish steel, the edges do not require sharpening.
Etched dies are made by dissolving the parts of a metal plate that are not needed, leaving only the parts that will become the blade. The protruding parts that remain are then polished. They are often referred to as pinnacle dies.
Finally, there are engraved dies, which are made by carving out of a block of metal using machinery. The descriptions of each type of die will follow in the subsequent sections.
When we talk about dies, this is it. The quintessential, the ‘king of the road’: the wooden die.
In this industry, wooden dies are referred to as ‘Thomson dies’ or ‘Vic dies.’ You may have heard the terms ‘Thomson cut’ or ‘Vic cut’; this is because wooden dies are commonly used for these types of cuts, hence the names.
Wooden dies are cheaper in terms of material costs and labor compared to other types of dies. It is accurate to assume that when referring to a ‘die’ in the context of paper die-cutting, it usually means a wooden die.
When using a wooden die for die-cutting, it cannot be processed as is; it always requires the application of ejection rubber. Ejection refers to the removal of the processed medium, such as paper, that has been embedded into the die. Without the ability to eject, it could lead to damage of the die. When looking at pictures of dies, you will often see green or blue materials attached; these are the ejection rubbers.
This leads to a discussion on the mechanics at the micro level, but the application of rubber is quietly important as it enables clean die-cutting. The type of rubber used and the method of application can vary, often reflecting the unique characteristics of each company.
When you think of a die for die-cutting, think of this wooden die. It’s best to understand that what cannot be done with this die is supplemented by other types of dies.
Shining in punching and bushing! The metal die
Metal dies are made from blocks of metal and are primarily used for punching and bushing. Punching and bushing are techniques often used for cutting out items like cards. Special machinery is required, and we do not have this equipment in our company.
Metal dies are generally made using the forging method. The production of metal dies is time-consuming, and because the steel material is expensive, the cost of the die is higher compared to wooden dies and others.
As a characteristic, metal dies can process thicker materials that other types of dies cannot handle. The type of die used varies depending on the processing medium and the volume of processing.
Leave the delicate and thin tasks to me! And the thick ones, you can count on me! That’s the etched die
Etched dies are used for die-cutting of intricate shapes and for cutting out stickers. They are made by corroding a metal plate and then creating the blade edge with a drill. They are also called Flexible Pinnacle Dies (commonly known as pinnacle dies). *Trademark of Tsukatani Hamono Manufacturing.
Etched dies have strengths such as being capable of processing ultra-thin materials and being used in high-speed processing machines for sticker roll-to-roll and cylinder processing (which we also do not have in our company). However, on the flip side, they have poor cutting quality, are not suitable for thick materials, are very expensive, and can also be considered as having low durability and being prone to damage.
Sharpest and most durable! The engraved die excels in both offense and defense without any weaknesses (but comes at a premium price)
Engraved dies are created by machining blocks of metal, such as stainless steel, using NC processing (Numerical Control machining) to produce the base and the blade. Compared to wooden or etched dies, they can produce dies with the highest precision.
Because they are made from materials with high hardness, engraved dies have excellent sharpness and durability, and can be used in combination with wooden dies, similar to etched dies. They can cut up to a blade height of 10mm, making them capable of processing thicker materials. Furthermore, a notable feature of engraved dies is that they can be re-sharpened.
As such, these dies excel in sharpness, durability, and precision, but as you can tell from the manufacturing process, they are very expensive and have long lead times. I think they are used for quite specialized applications unless it’s a situation where other dies just won’t do the job! Remembering them as a last resort when you’re at a ‘Help, nothing else works!’ moment would be good.
How was that? Customers don’t often specify the type of die, but having such knowledge can be helpful when talking to die-cutting companies like ours!